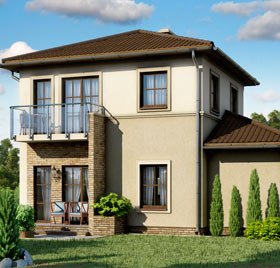
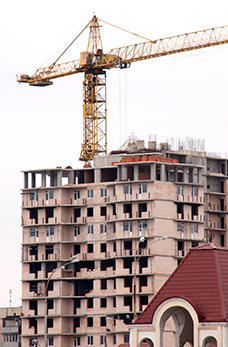
Infolab.ru - Инфолаб - Статьи - Методы защиты от коррозии
Опубликовано: 02.10.2018
Методы защиты от коррозии
В зависимости от вида коррозии и причин её возникновения используются различные методы защиты. Выбор способа защиты от коррозии определяется его эффективностью в данном конкретном случае, а также экономической целесообразностью применения.
Легирование.С целью предотвращения коррозии создаётся большое число нержавеющих сталей путем присадок к железу никеля, хрома, кобальта и др. Такие стали называются легированными, они не покрываются ржавчиной; тем не менее, хоть и с небольшой скоростью, но они подвержены поверхностной коррозии. В то же время, следует учитывать тот факт, что при использовании легирующих добавок коррозионная стойкость меняется скачкообразно.
Нанесение защитных лакокрасочных покрытий.Одним из наиболее часто применяемых способов защиты металлических поверхностей от атмосферной коррозии является нанесение на их поверхность защитных пленок самого разного вида: лака, краски, эмали, других металлов. Наиболее доступным и простым способом является нанесение лакокрасочных покрытий. Лаки и краски имеют низкую газо- и паропроницаемость, обладают водоотталкивающими свойствами, поэтому они препятствуют доступу к поверхности металла воды, кислорода и содержащихся в атмосфере агрессивных компонентов. Окраска поверхности металла не исключает коррозию, а служит для нее лишь преградой. Надёжность этой преграды определяются: толщиной слоя покрытия, пористостью, равномерностью, проницаемостью, способностью набухать в воде, прочностью сцепления с поверхностью (адгезией).
Качество покрытия зависит не в малой степени от тщательности подготовки поверхности, а также способа нанесения защитного слоя. Окалина, ржавчина должны быть удалены с поверхности покрываемого металла. Необходимо также, чтобы поверхность была предварительно обезжирена. Всё это служит для хорошей адгезии покрытия с поверхностью металла. Для качественной подготовки поверхности металла под окраску существует множество различных способов. Одним из современных способов подготовки поверхности является плазменная обработка . Помимо основной функции, очистки поверхности перед окрашиванием, плазменная обработка увеличивает свободную энергию поверхности (СЭП) материала, что, в свою очередь, приводит к улучшению смачиваемости и адгезии этой поверхности.
В свою очередь, для снижения смачиваемости водой, лакокрасочные покрытия иногда защищают восковыми составами или кремний-органическими соединениями. Как уже было отмечено выше, лаки и краски наиболее эффективны для защиты от атмосферной коррозии. В большинстве случаев они непригодны для защиты подземных сооружений и конструкций, так как трудно предупредить механические повреждения защитных слоев при контакте с грунтом. Как показывает опыт, срок службы лакокрасочных покрытий в подземных условиях невелик, поэтому принято для данных целей применять толстослойные покрытия из каменноугольной смолы (битума).
Стоит отдельно отметить, что в некоторых случаях пигменты красок выполняют также роль ингибиторов (т.е. замедлителей) коррозии. К числу таких пигментов относятся хроматы стронция, свинца и цинка (SrCrO4, PbCrO4, ZnCrO4).
Грунтовки и фосфатирование.Часто под слой лакокрасочного покрытия наносят грунтовки. Пигменты, входящие в состав грунтовки, должны обладать ингибиторными свойствами. Проходя через слой грунтовки, вода растворяет некоторое количество пигмента и становится менее коррозионноактивной.
Вместо грунтования иногда проводят фосфатирование поверхности металла. Для этого на чистую поверхность кистью или распылителем наносят растворы ортофосфатов железа (III), марганца (II) или цинка (II), содержащих и саму ортофосфорную кислоту H3PO4. В заводских условиях фосфатирование ведут при 99-97°С в течение 30-90 минут. В образование фосфатного покрытия вносят вклад металл, растворяющийся в фосфатирующейся смеси, и оставшиеся на его поверхности оксиды.
Пленка фосфатов защищает поверхность изделия от атмосферных осадков, но мало эффективна от растворов солей и даже слабых растворов кислот. Поэтому фосфатная пленка может служить лишь грунтом, обеспечивающим хорошее сцепление краски с металлом, для последовательного нанесения органических защитных и декоративных покрытий - лаков, красок, смол.
Электрохимическая защита (снижение коррозии наложением внешнего тока)Защита металла от коррозии, осуществляемая поляризацией от внешнего источника тока или путем соединения с металлом (протектором), имеющим более отрицательный или более положительный потенциал, чем у защищаемого металла. В зависимости от направления поляризации различают катодную и анодную защиты. (ГОСТ 5272-68)
К электрохимической защите относят: - анодную защиту, при которой электродный потенциал сдвигают в положительную область до таких значений, когда на поверхности металла образуются т.н. пассивирующие слои (т.е. слои повышенной стойкости); - катодную защиту, при которой потенциал металла сдвигают из области активного растворения в более отрицательную область относительно потенциала коррозии.Катодная защита применяется для защиты от морской коррозии. Гражданские суда защищают с помощью Аl-, Mg- или Zn-протекторных анодов, которые размещают вдоль корпуса судна и вблизи от винтов и рулей. Особенно важно использование катодной защиты для стационарных нефтегазопромысловых сооружений, трубопроводов и хранилищ на континентальном шельфе. Подобные сооружения не могут быть помещены в сухой док для восстановления защитного покрытия, поэтому электрохимическая защита является основным методом для защиты от коррозии. Катодную защиту, как правило, совмещают с нанесением защитных покрытий.
Анодная защита используется в химической и смежных с ней отраслях промышленности. Широко применяют анодную защиту для оборудования, работающего в среде серной кислоты, водных растворах аммиака и минеральных удобрений, фосфорной кислоты. Особенно важна анодная защита теплообменного оборудования из легированных сталей в производстве серной кислоты. Защита холодильников от агрессивного воздействия кислоты позволяет повысить рабочую температуру, интенсифицировать теплообмен, повысить эксплуатационную надежность.
Силикатные эмалевые покрытияЭмалирование поверхностей осуществляют в несколько этапов. Сначала на очищенную поверхность наносят грунтовочный слой в виде водной суспензии и обжигают его в печи. Затем наносят слой покровной эмали и повторяют обжиг. После контроля качества получившегося защитного слоя в случае необходимости процедуру повторяют с нанесением эмали на забракованные участки.
Наиболее распространены стекловидные эмали - прозрачные или загашенные. Их компонентами являются SiO2 (основная масса), B2O3, Na2O, PbO. Кроме того, вводят вспомогательные материалы: окислители органических примесей, оксиды, способствующие сцеплению эмали с эмалируемой поверхностью, глушители, красители. Эмалирующий материал получают сплавлением исходных компонентов, измельчением в порошок и добавлением 6-10% глины. Эмалевые покрытия в основном наносят на сталь, а также на чугун, медь, латунь и алюминий.
Хорошо известный метод нанесения эмали в настоящее время все чаще используется для изготовления химического оборудования. Эмалированные поверхности, создаваемые на углеродистой или нержавеющей стали, отличаются высоким показателем коррозионной устойчивости (на уровне стекла) и в то же время низким коэффициентом температурного расширения. Такие поверхности являются не только антипригарными, но и инертными к большинству из известных активных сред.
Эмали обладают высокими защитными свойствами, которые обусловлены их непроницаемостью для воды и воздуха (газов) даже при длительном контакте. Их важным качеством является высокая стойкость при повышенных температурах.
Благодаря вышеперечисленным свойствам, эмалированные покрытия идеально подходят для изготовления эмалированных химических реакторов , перемешивающих устройств, теплообменных аппаратов, абсорбционных и ректификационных колонн различной, различных ёмкостей для химических реакторов.
К основным недостаткам эмалевых покрытий относят чувствительность к механическим и термическим ударам. При длительной эксплуатации на поверхности эмалевых покрытий может появиться сетка трещин, которая обеспечивает доступ влаги и воздуха к металлу, вследствие чего и начинается коррозия. К сожалению, ремонт этих дефектов достаточно затруднителен и связан с повторным нанесением защитного покрытия на повреждённые места и последующим обжигом, что в условиях удалённости от предприятия - изготовителя просто неосуществимо. Поэтому решающее значение имеет выбор производителя химического эмалированного реактора и качество его изготовления.
Цементные покрытияДля защиты чугунных и стальных водяных труб от коррозии используют цементные покрытия. Защитные свойства цементных покрытий обеспечиваются двумя свойствами цемента. Первое - это химическая щелочная реакция цемента и второе - это постепенное уменьшение объёма воды, находящейся в контакте с чугуном. При заполнении водой трубы с цементно-песчаным покрытием, вода проникает в поры покрытия, высвобождая значительное количество гидрата кальция. Гидрат кальция вступает в реакцию с бикарбонатом кальция, содержащимся в воде с выпадением в осадок карбоната кальция, что приводит к закупориванию пор в растворе и предотвращает дальнейшее проникновение воды. Вода, проникшая через покрытие и вступившая в контакт с железом, растворяет часть железа, но свободная известь вызывает выпадение железа в виде гидроокиси, что также забивает поры в цементе. Аналогичным образом, сульфаты выпадают в виде сульфата кальция. Благодаря этим реакциям, покрытие обеспечивает как физический, так и химический барьеры для агрессивной воды. Поскольку коэффициенты теплового расширения портландцемента и стали близки, то он довольно широко применяется для этих целей.
Недостаток портландцементных покрытий тот же, что и эмалевых, - высокая чувствительность к механическим ударам. Кроме того, цементно-песчаные покрытия обладают повышенной шероховатостью и ощутимо уменьшают площадь поперечного сечения труб, что приводит к увеличению гидравлического сопротивления и снижению пропускной способности трубопроводов.
Нанесение покрытий из металловОдним из широко применяемых способов защиты металлов от коррозии является покрытие их слоем других металлов. Покрывающие металлы сами подвержены коррозии в меньшей степени, так как покрываются плотной защитной оксидной пленкой.
Покрывающий слой может быть нанесён различными методами: горячее покрытие - кратковременное погружение изделия в ванну с расплавленным металлом; гальваническое покрытие - электроосаждение из водных растворов электролитов; Гальванические покрытия характеризуются хорошим сцеплением с основным металлом, сравнительно высокими защитными свойствами, высокими механическими свойствами, стойкостью по отношению к органическим растворителям. К недостаткам следует отнести появление хрупкости в основном металле и неравномерность толщины покрытия на различных участках деталей. металлизация - напыление; диффузионное покрытие - обработка порошками при повышенной температуре в специальном барабане;Имеются и другие методы нанесения металлических покрытий. При использовании любого из методов решающее значение при оценке качества полученного покрытия имеет предварительная подготовка поверхности. Одним из способов подготовки поверхности является плазменная обработка
Вернуться к списку статей.